Altri implements the Kaizen method at its industrial units
This Japanese method aims to help companies from all business sectors to grow their sales, increase profitability and improve their return on investments by implementing a policy of continuing improvement.
In Japanese kai means to change and zen means for the better. When you put these two words together you get kaizen, meaning continuing improvement. This business concept was introduced into Europe in 1986, when professor Masaaki Imai wrote his book Kaizen: The Key to Japan’s Competitive Success. The Kaizen philosophy is geared towards improving industrial production. The practice is recognised all around the world as an important pillar in organisations’ long-term competitive strategy. Toyota’s production line in Japan is a perfect example of how an organisation can see substantial improvements by applying the Kaizen method.
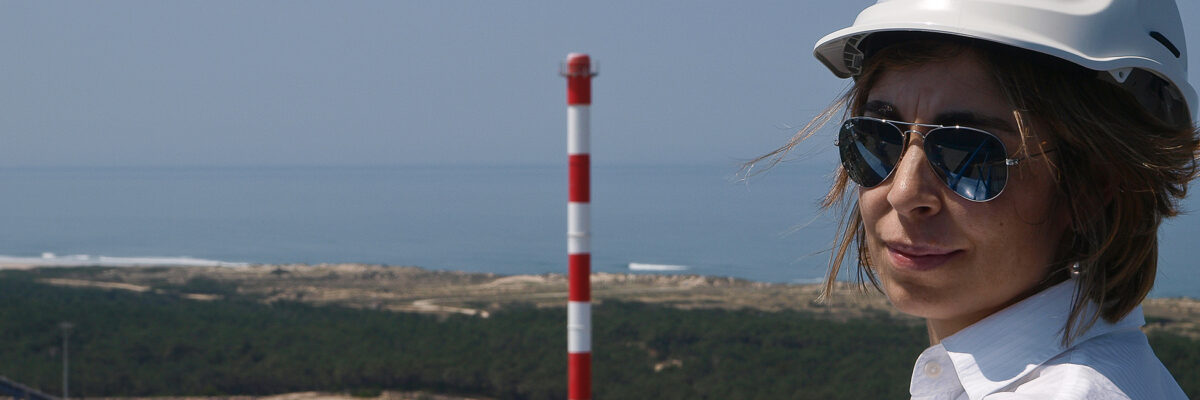
Although linked with industrial production, the concept of continuing improvement can be applied to other sectors of business activity such as health, finance and retail, among others. There are several success stories which validate Kaizen. Zara, the ready-to-wear chain, is one such case, having become one of the world’s most successful high street brands, producing around 40% of its product-lines in Europe. Other multinationals have also employed the concepts of Kaizen and achieved results which have become worldwide case studies. Bosch, Porsche and Honeywell are other very successful examples.
Portugal also has good examples which are worthy to note. Every year the Kaizen Institute Portugal recognises organisations with stand-out performances nationally. The Kaizen Lean Award is given to organisations which prove themselves to be excellent examples of good continuing improvement practices. The awards categories are Excellence in Productivity, Excellence in Quality, Excellence in the Continuing Improvement System and Excellence in Growth Strategy.
Celbi scoops Kaizen Institute award
The 8th edition of the Kaizen Lean Awards was held on April 9th at the Champalimaud Foundation, and Celbi was one of the night’s big winners with the top award in the Excellence in Quality category, for its Improve Quality to Increase Operating Efficiency Project.
The results obtained show improved product quality, lower pulp production losses and consequently better availability of the installation, a 6% reduction in electricity consumption, a 19% decrease in specific water use, and increased lifespan of timber shredding blades. These gains contributed towards a 3% rise in operating efficiency and increased production/sales.
As well as these tangible gains, Celbi won an award for its good continuing improvement practices. The award from the Kaizen Institute is recognition for our attitude of going above and beyond, for doing the right thing, to achieve more and better results. We are the continuing improvement, every day and everywhere.
Sofia Reis Jorge, Celbi’s director of Technical Control and Management Systems, says that this award is “recognition for our attitude of going above and beyond, for doing the right thing, to achieve more and better results”.
The award is also proof that the Lean methods are capable of being successfully implemented “in process manufacturing businesses, and not just in discrete manufacturing such as the automobile industry”.
Application of the knowledge gained
The project started in 2016 with two pilot teams, a Gemba (operational) team and a supervisory team. Using the results obtained during this stage and the lessons learned, the methodology was extended in 2017 to the entire industrial area, involving around 210 employees, 2,387 hours of training and 28 team boards implemented.
It all started a few years ago, when Celbi looked at its strategic plan and identified that there was a need to implement a Lean Management method. According to Sofia Reis Jorge, “the Kaizen Institute had a good portfolio of companies with which it worked and we liked its working method, so we felt it was the most suitable partner which was most in line with the goals set out by the company”.
It was therefore an obvious choice for Celbi to go ahead with a project which, from an operational standpoint, aimed to ensure continuing improvement of quality in order to achieve increased operating efficiency. Sofia Reis Jorge states that: “All of the organisation’s hierarchical levels were involved, executing projects with multidisciplinary teams. The end result translated into increased pulp production due to losses and inefficiencies having been reduced, without adversely affecting the quality of the end product. The teams are working better and more in line with the company’s strategic goals.”
All 210 employees from Celbi’s industrial area were involved in this process in order to get to the end result, coordinated by the Management Group which comprised the Industrial Administrator and the five directors who manage the company’s industrial business activity, with support provided by the Management Systems and Continuing Improvement coordinator.
The implementation of the Kaizen principles within the Altri Group is not limited to Celbi. There are other continuing improvement projects at Caima and at Celtejo.
Celtejo identified 16 projects for improvement
As the saying goes: “There’s a right time for everything.” Following the recent investments made at Celtejo which included a new recovery boiler, a new Industrial Waste Water Treatment Plant (IWWTP), a new turbine and a new water treatment installation, it felt like the right time to take a major step forward in continuing improvement, by implementing the Kaizen tool.
Since human capital is one of the group’s main assets, it is vitally important for everyone to feel as if they are part of the whole, contributing towards improving the results achieved by their team. The implementation of the Kaizen tool is therefore one more resource to reinforce the continued search for improvement in the bond between employee and company.
The aim in introducing Kaizen practices at Celtejo is to endow the organisation with new and better solutions with which waste and shortfalls will be reduced, thereby increasing productivity and consequently results.
Kaizen is based on a specific method, whose main tool is the PDCA Cycle, meaning Plan, Do, Check, Act, representing each stage: Plan – the initial stage identifying, observing and analysing the problems found; Do – after planning, actions must be put into practice in order to achieve the goals of the previous stage; Check – Note the actual effects which were achieved during the actions undertaken, whether everything was executed as planned and/or whether there were any shortfalls; Act – if the results achieved are not those planned, new actions should be drawn up. In the event of a satisfactory result, this stage serves as a preventative action to ensure that the shortfall isn’t repeated. This cycle is easier to understand if viewed as a constantly rotating circle.
Although the Kaizen tool is still a recent phenomenon at Celtejo, all the teams on the ground (Gemba) have joined in enthusiastically, promoting improvements which will streamline their work. 16 projects for improvement have been identified for analysis.
Creating simple tools
Did you know that visual management can be a useful tool in current monitoring of processes and for quick and reasoned decision-making? This was the theme that pushed the continuing improvement team, which is responsible for implementing the Kaizen method at Caima, to create tools such as the Did you know…? devices, the OPLs – One Point Lessons and the Non-Conformity cards.
During the stage when all Caima’s teams were already using the methodology implemented in May 2018, the Daily Kaizen N1 and Kaizen N2 (5 S) meetings held demonstrated the need to improve aspects relating to exchanging and ensuring the uniformity of information and to monitor improvement actions. A series of simple tools was devised to this end, which revolutionised productivity, process efficiency, maximisation of resources and team motivation.
The aim of the Did you know…? device is to ensure that the information is more transparent and transversal, by using small cards containing simple pieces of information on topics which are of interest for the daily running of the factory. OPLs – One Point Lessons were created to make it quicker to pass on information. These documents transcribe procedures and information in a manner which is simple and accessible to all, and guarantee access to this information.
The Kaizen tools were incorporated into the Management system using Improvement Cards, Help Chain Cards, the recently-implemented Kobetsu Projects and Non-Conformity Cards in existing processes.
In order to follow up on the Non-Conformities identified in the internal audit of the laboratory, the management started by creating new models of cards so as to make the non-conformity more highly visible to the team, as well as the corrections and corrective actions taken, and also the deadlines and personnel in charge of implementation. From there, this methodology was rolled out to the entire system and organisation.
Kobetsu projects are when improvements are studied and implemented, pertaining to complex problems which require monitoring by multidisciplinary teams, with more simple problems earmarked to be solved via the PDCA cycle, using Improvement Cards and Help Chain Cards, or via the task schedule when they can be resolved immediately.
The incorporation of Kaizen tools in the Management Systems and in Caima’s daily operation has proven to be an asset and a veritable cultural revolution.