The energy that move us
Our industry has, throughout the decades, been faced with challenges which force companies to reinvent themselves. The evolution of the sector and its ability to remain profitable have been determined by how we use energy. This has been the key to its success. Now we are being called upon to deal with global challenges whose impacts reach beyond our sector. What role might we play? And how does this relate to the energy that moves us?
By Gualter Vasco
Director of Digital Transformation and Asset Management at Altri
The first cellulose fibre factories were mostly dependent upon steam, both as a thermal energy source and to provide energy to drive machinery; wood and coal were the main sources of primary energy.
The gradual electrification of industry from the end of the 19th Century brought with it huge efficiency gains: the development of the electric motor allowed steam engines to be replaced and the use of fuels to therefore be reduced, and innovations to the electric generator enabled factories to generate their own electricity. Thanks to the War of the Currents between Westinghouse and Edison, industry as a whole took a few steps forwards and the cellulose fibre industry was no exception. Generators had mostly been water-powered, but steam turbines quickly took on an increasingly important role. It was around this time that petroleum was discovered, and the first commercial oil wells began operation in the USA, ushering in a new era.
Petroleum revolutionised industry, not only as an energy source but it also led, for example, to the development of lubricants needed for the increasingly large and more complex machinery. Another factor was the new industries which sprang up from products manufactured from oil. From an energy standpoint, industry started switching from the energy sources then in use – which were almost exclusively renewable – to oil-derived fuels.
The industrial growth and economic expansion which followed has created new challenges. Competition between peers forces companies to focus more attention on how they use resources, including energy. Industrial processes are adapted to make better use of heat and the combined production of heat and electricity – cogeneration now tends to be the rule.
The next major leap forward occurred during the 1930s with the invention of the recovery boiler for the kraft process; this milestone – arguably the most important in the history of cellulose production – virtually closed the cooking cycle, and in addition to enabling inorganic materials to be recovered and thermal energy to be generated to fuel a major portion of the factories’ needs, it also meant a very significant reduction in the environmental impact caused by the factories. G.H. Tomlinson’s invention was motivated by desire to recover chemicals, but his work actually had a disruptive impact on the energy profile of pulp mills by directly improving companies’ profitability and thereby encouraging the growth of the sector, leading to the widespread use of the kraft process and consigning other chemical pastes to niche markets. The cellulose industry’s expansion following the Second World War, very much driven by demand from and economic growth of the west, did not pay heed to what are now considered indisputable values. Efficient use of resources, sustainability and circularity were way down the list of priorities and were only very occasionally taken into consideration. Up until the first oil shock in 1973. Exactly 50 years ago, as a result of the Yom Kippur War, a coalition of Arabic countries proclaimed an embargo on oil exports to the west, leading to prices rocketing which reverberated throughout the global economy. Rising production costs – caused directly by energy costs and indirectly by higher chemical prices – forced the cellulose industry to re-think its processes.
Alternatives to petroleum-derived chemicals
The search was on for alternatives to petroleum-derived chemicals and those whose production is oil-dependent, and also for alternatives to fossil fuels. With regard to chemicals, there was not much to be done other than optimising their use by reducing consumption and recovering as much as possible. The search for fossil fuel alternatives, however, saw the emergence and gradual spread of renewable fuels, particularly biomass, wood waste and other forest residues. Many factories brought their coal-powered oilers back into service or adapted fuel-oil boilers to burn these “new” fuels, although mostly in ways which were far from being the most efficient.
But in times of war, they had to make do. In the final decades of the 20th century, more effort went into
developing technological solutions to ensure efficient energy production from biomass. It should be pointed out that for most of the industry, the term “biomass” encompasses waste wood, sawdust and bark, as well as forest residues. This period saw great improvements in boiler performance; it became possible to burn more challenging biomass more efficiently, and there was an expansion of the range of waste products which could be used.
Altri is committed to decarbonizing industrial operations, by liminating fossil fuels as a primary energy source by 2030.
Parallel development paths opened up and solutions emerged for the gasification of such fuels, to offer solutions to clients unable or unwilling to invest in new boilers, so that they too could have an alternative to fossil fuels. Nevertheless, these options were not broadly taken up and even today most pulp manufacturers choose to use biomass boilers.
This is a brief summary of the path that has brought us where we are today. Throughout our industry’s 150-year history we have seen that energy matters can be addressed by solutions, techniques or simple business restructuring to respond to issues relating to our environmental or social impact or just to keep production costs under control to guarantee the profitability required to keep mills in operation.
Business profitability is an ever-present concern. Unprofitable companies wither and die. But beyond this obvious problem, today we have to deal with strict environmental and sustainability demands. We are required to put together fossil fuel replacement plans and improve our sustainability performance. The global targets are tough. All of us – citizens and companies alike – have to combat climate change. How can we contribute towards this global cause?
Can what brought us here, take us further?
These goals are certainly ambitious and will force us, in some cases, to implement solutions which aren’t yet commercially available or for which there are few examples to study.
The primary goal seems easy: we just have to cut consumption and increase production. We should continue to optimise operations to reduce consumption and seek out ways to increase generation. To achieve the increments as per our commitment, we are going to have to keep investing in generation for self-consumption. We have almost finished installing production units equipped with PV panels at all our factories and in the Viveiros do Furadouro tree nurseries. In total, these UPACs will account for over 15MW of the installed power and will contribute decisively towards reaching our goal, insofar as the increased amount injected into the grid will equate to the UPAC energy produced. This solution will probably be expanded, with more panels installed at our factories and elsewhere.
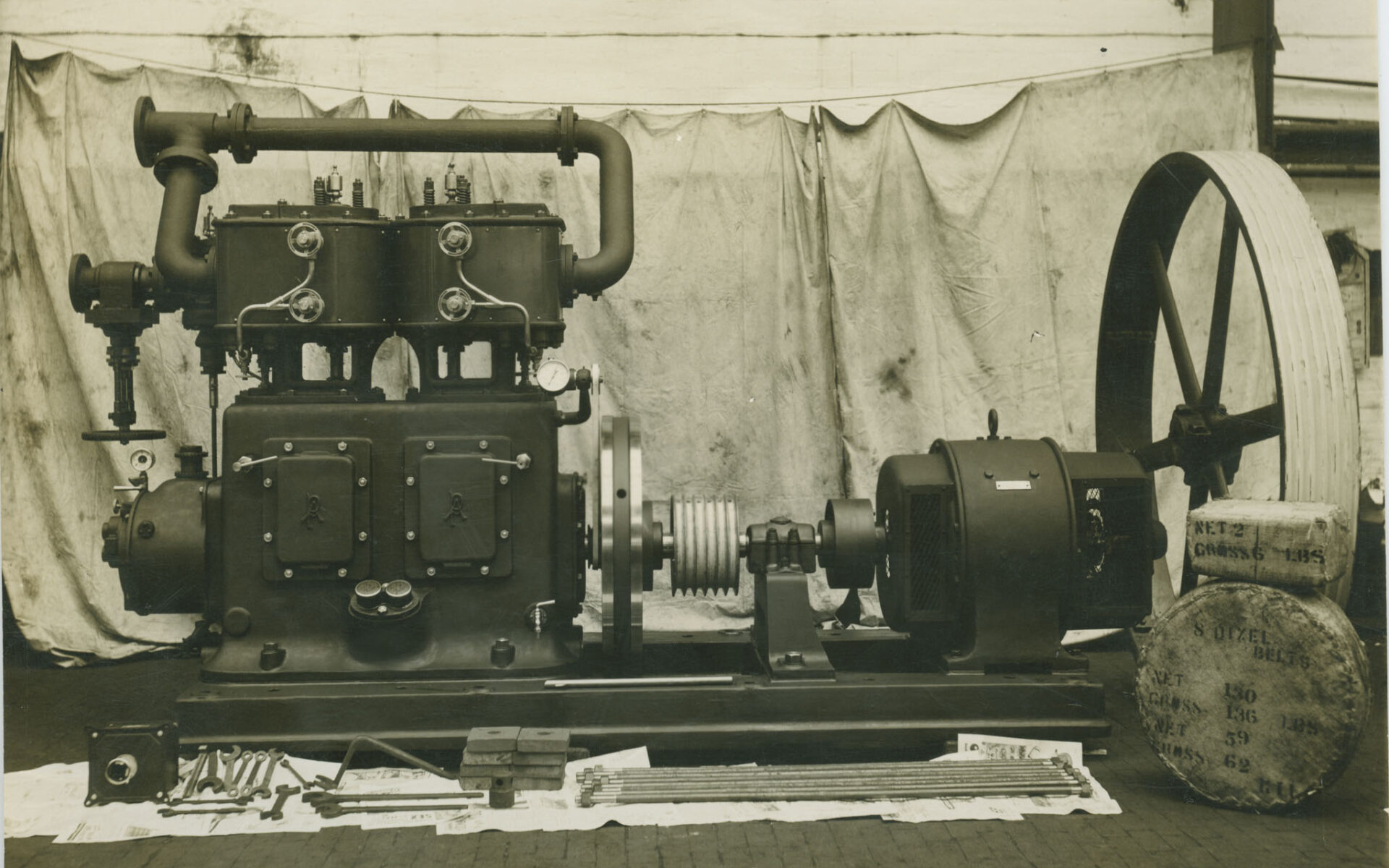
In terms of decarbonisation, however, the solutions are less obvious. At least for Biotek and Celbi. In order to decarbonize these two factories, we need to find renewable fuels to power the lime kilns, which represent just over 90% of the total fossil fuel consumption each. Caima does not have a lime kiln and with the new biomass plant coming on line it will no longer require natural gas. By the end of 2023 it will be the first Portuguese (and probably European) factory to be fossil fuel free.
Several options are available to replace the fossil fuels we currently use in our mills
There are several examples which use timber as fuel, either where the timber is gasified and then the synthesis gas burnt, or where it is directly burnt after being chipped and pulverised.
These solutions are fairly commonplace in regions where wood or wood waste is abundant, such as in South America and Scandinavia. It is common knowledge that there is a lack of wood for paste in Portugal, so what wood there is has to be used for this purpose. Furthermore, these solutions require heavy investment in machinery.
Another solution which is somewhat common and easily applied, is to burn factory-produced methanol. This method doesn’t usually raise any major difficulties and may contribute greatly towards decarbonisation. Methanol already represents around 15% of the primary energy used to fuel the kiln at Celbi, and this solution is being studied at Biotek, where methanol is not extracted. These solutions that are based on using existing local resources appear to be the easiest to implement.
A different approach is to use lignin as fuel. The most well-known method is commercially known as Lignoboost and allows the lignin to be extracted in solid form, thereby enabling it to be sold on the chemical industry market or used as fuel. There are some known examples, but the high costs of investing in both the lignin production facility and in adapting the kiln firing systems render this solution unappealing. Another alternative that is increasingly being talked about is hydrogen burning. Hydrogen is clearly going to play a key role in decarbonising the economy. In our specific case, it can be used as furnace fuel, but with some limitations. Its flame temperature is substantially higher than that of natural gas, which means additional precautions need to be taken, both in terms of controlling the process and monitoring the effects on the kiln materials; special refractories are needed and the metallurgical properties of the metals involved have to be taken into consideration. The examples known are mainly facilities where hydrogen is available as a by-product, resulting from the on-site production of other chemicals, and these examples show that up to 30% of the kiln’s needs can be met by burning hydrogen.
Green hydrogen is produced by water electrolysis using renewable electricity and can be used as a fuel, as a method of storing energy or to be injected into the natural gas network, or even to produce other renewable fuels. European policies in matters of decarbonisation foster projects to produce hydrogen and inject it into the national natural gas network in quantities which will enable widespread use, meaning that all consumers of natural gas will also be consumers of green hydrogen.
Another green fuel which can be a substitute for natural gas is biomethane. Biomethane is simply methane gas produced from renewable sources, usually via the anaerobic digestion of agricultural (crops and livestock) waste, leftover foods or organic WWTP sludge. Waste resulting from such digestion can be used directly as an agricultural fertiliser. Caima has been using this technology since 1991 to treat part of its effluent, producing biogas which fires its boilers. Biomethane is a direct replacement for natural gas and its use does not require any alterations to the existing facilities, hence one possible means of decarbonising our operations may be to develop biomethane production projects; implementing such projects close to the factories may create synergies where, for example, factory sludge is used as a raw material. This technology is already in place and there are thousands of facilities of this kind in Europe.
Most European states currently have ambitious plans to expand biomethane production. In some countries, it accounts for a very significant percentage of the gas consumed. The solutions set out above could be part of the roadmap for the decarbonisation of our industrial operations, thereby allowing us to achieve our targets. It involves projects of varying degrees of complexity, encompassing technologies at different levels of maturity and requiring significant amounts of investment.
Altri’s role in decarbonisation issues does not end with replacing the fossil fuels used in our factories with green fuels. We can participate more globally and contribute towards other sectors of the economy finding alternatives leading to their decarbonisation. A particularly difficult sector is transport; despite the increased percentage of electric light passenger vehicles, the electrification of aviation or large container ships is nowhere on the horizon. Renewable replacement fuels need to be found for these sectors, which can be used for fleets already in operation.
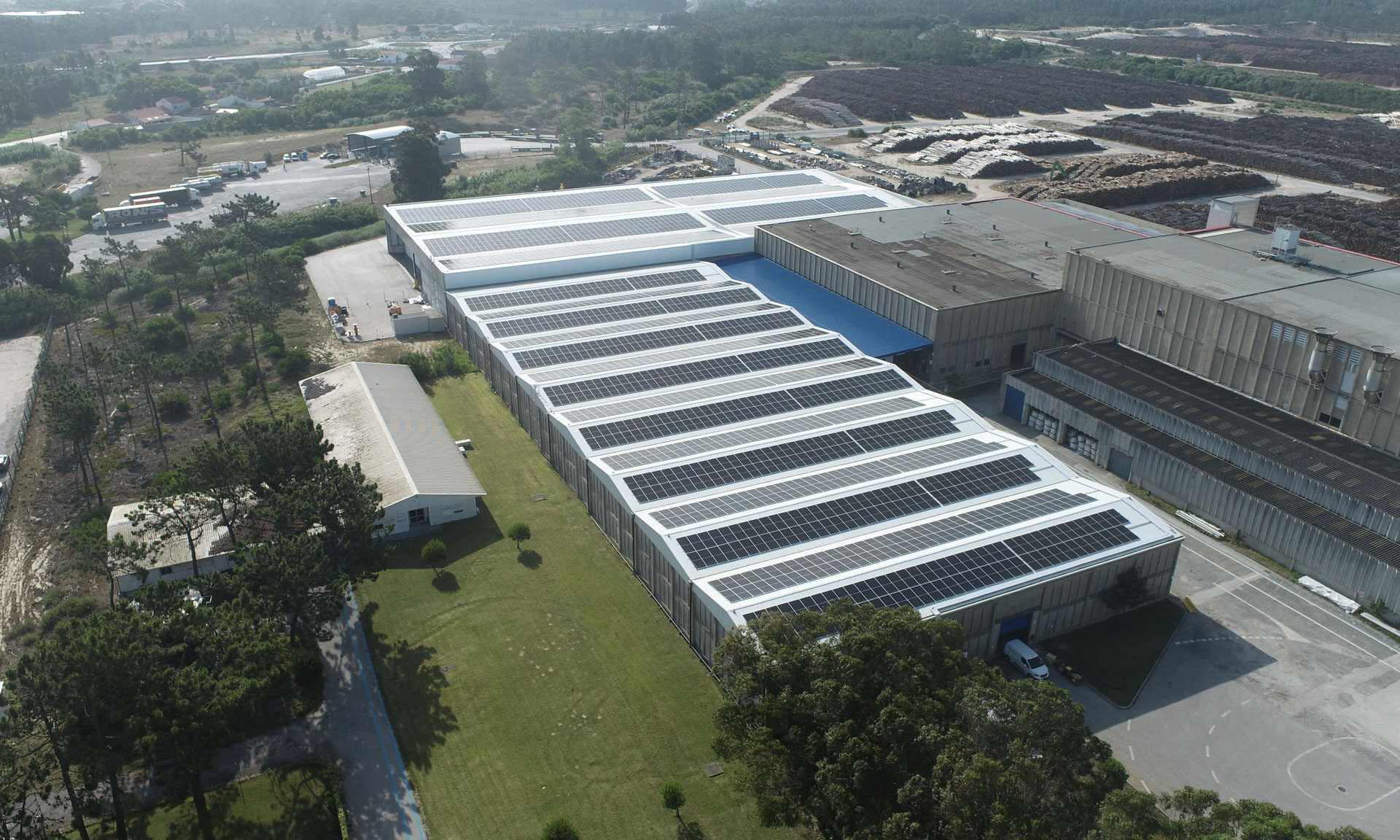
The solution entails producing synthetic fuels, or e-fuels. These fuels are produced using green hydrogen and green CO2, captured, for example, from smoke and fumes from a recovery boiler or biomass boiler; different chemical reactions can be used to create fuels which can be a direct replacement for jet-fuel, petrol or diesel. Projects of this kind have been announced throughout Europe, chiefly for the production of SAF – Sustainable Aviation Fuel or e-Methanol geared towards the shipping sector. Our factories are sources of green CO2 and could be anchors for projects of this nature, which are extremely complex and entail investments of hundreds of thousands of euros.
An e-methanol production facility, for example, installed next to one of our factories could generate beneficial synergies for both. As well as providing CO2, we could use the final effluent to produce hydrogen or BP steam or hot or cold water; hydrogen production generates surplus oxygen, much more than normal factory consumption, which as well as its usual applications can, for example, be used in aeration at the WWTP thereby allowing the number of used compressors to be reduced, or mixed into the boiler or kiln combustion air, leading to lower ventilator consumption. Finally, we could use part of the hydrogen or e-methane produced to supply the kiln, instead of natural gas.
My aim here has been to provide a brief outline of the options available to help us in this marathon. At Altri we are committed to achieving the goals we have set, and we are aware of our role within the community. We feel it is our obligation to be part of the solution to rise to the challenges facing society. And once again we are having to reinvent ourselves. And once again the solution could be based on the energy that moves us.